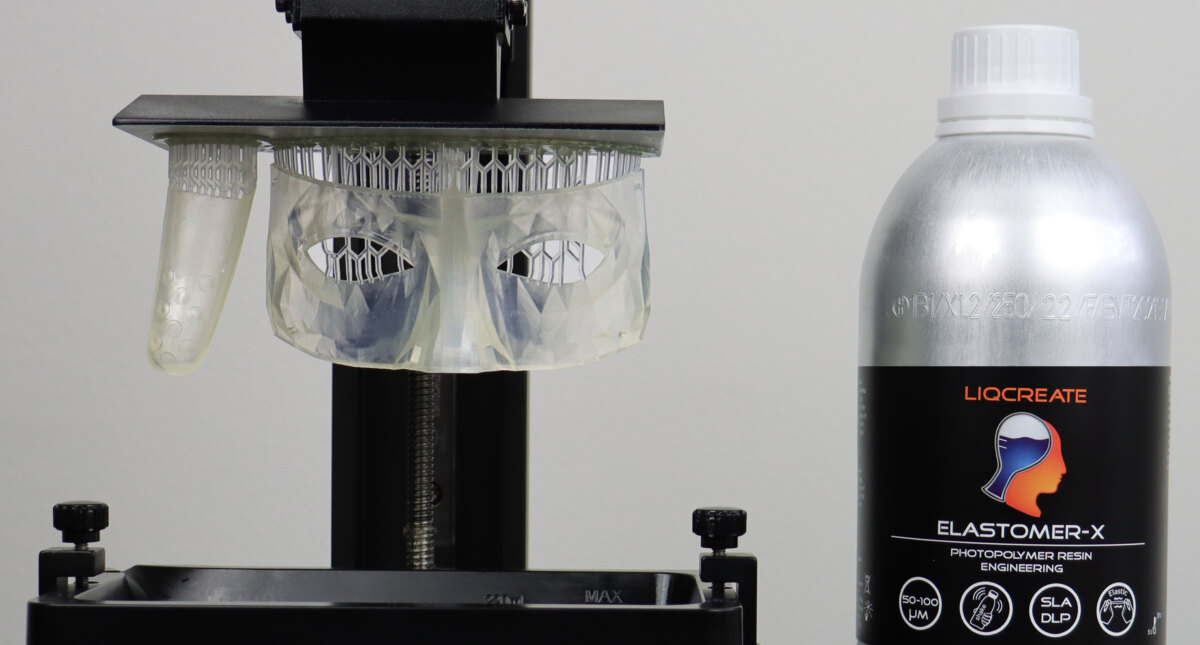
🧩 Lesson: Stereolithography (SLA)
✅ Summary
Stereolithography (SLA) is a resin-based 3D printing technology that uses ultraviolet (UV) light to cure liquid photopolymers, creating detailed models layer by layer. Known for its high resolution and exceptional surface finish, SLA is ideal for applications where fine detail and accuracy are critical. In this lesson, we’ll explore the SLA printing process, its strengths and weaknesses, and the use-cases where it shines.
🎯 Learning Objectives
By the end of this lesson, learners will be able to:
-
Explain how the SLA 3D printing process works
-
Identify the components of an SLA printer
-
Understand the post-processing steps required after printing
-
Evaluate the strengths and limitations of SLA technology
-
Identify common applications of SLA printing in various industries
📘 Lesson Content
🔍 1. How SLA Works
1.1 Introduction to Photopolymerization
SLA relies on photopolymerization, a process in which UV light triggers chemical reactions that solidify a liquid resin into a solid structure. Unlike filament-based printing (FDM), SLA uses a focused light source to cure each layer with high precision.
1.2 Design Preparation
-
A 3D model is created in CAD software and exported as an STL/OBJ/3MF file.
-
Slicing software (like PreForm, Chitubox, or Lychee) converts the model into thin horizontal layers and generates a print file with laser path instructions.
1.3 SLA Printer Components
Component | Function |
---|---|
Resin Tank | Holds liquid photopolymer resin |
Build Platform | Moves vertically (Z-axis) to support layer growth |
UV Laser | Cures the resin by tracing the layer shape |
Galvanometers | Mirrors that aim the laser across the resin surface |
1.4 Layer-by-Layer Printing Process
-
The build platform lowers into the resin tank, leaving a small gap.
-
The UV laser is directed to trace and cure the first layer of the print.
-
The platform rises slightly, and resin flows underneath the cured layer.
-
The process repeats layer by layer until the part is complete.
1.5 Post-Processing
-
Washing: Prints are removed from the platform and washed (typically with isopropyl alcohol) to clean uncured resin.
-
Post-Curing: Printed parts are exposed to additional UV light to strengthen and stabilize the material.
-
Support Removal: Supports are manually removed and often sanded to smooth the surface.
🧪 2. SLA Strengths and Weaknesses
✅ Strengths
Feature | Benefit |
---|---|
High Resolution | Produces extremely fine details and sharp edges |
Smooth Surface Finish | Minimal layer lines, great for cosmetic models |
Complex Geometries | Can print intricate designs, thin walls, and undercuts |
Material Options | Resins with varying properties: flexible, transparent, heat-resistant |
Ideal for Prototyping | Quick, high-quality prints for form and fit testing |
❌ Limitations
Limitation | Impact |
---|---|
Material Fragility | SLA parts are often more brittle than FDM or SLS prints |
Post-Processing Time | Requires washing, curing, and support removal |
Limited Build Volume | Smaller max print size than FDM printers |
Cost | Resin, equipment, and cleaning supplies add up |
Safety Concerns | Resins are toxic and require protective gear and ventilation |
🧩 3. Use Cases and Applications of SLA
Application | Why SLA is Ideal |
---|---|
Prototyping | Excellent for visual and tactile prototypes in product design and engineering |
Dental and Medical | Precision for dental aligners, surgical guides, hearing aids |
Jewelry Design | High-resolution wax-like prints for casting or design approval |
Miniatures & Figurines | Sharp, smooth features for gaming and collectibles |
Education | Demonstrates detailed models of complex structures |
Art & Sculptures | Enables expressive and intricate creations with high fidelity |
Tooling & Molds | Short-run or prototype molds for casting or injection forming |
🧠 4. Summary
SLA printing offers exceptional detail and surface finish, making it a go-to technology for high-resolution prototyping, artistic applications, and precision components. However, its higher cost, material limitations, and post-processing requirements must be factored in when choosing it for a specific project.